1: The Elimination of Planter Pinch-Row Yield Loss
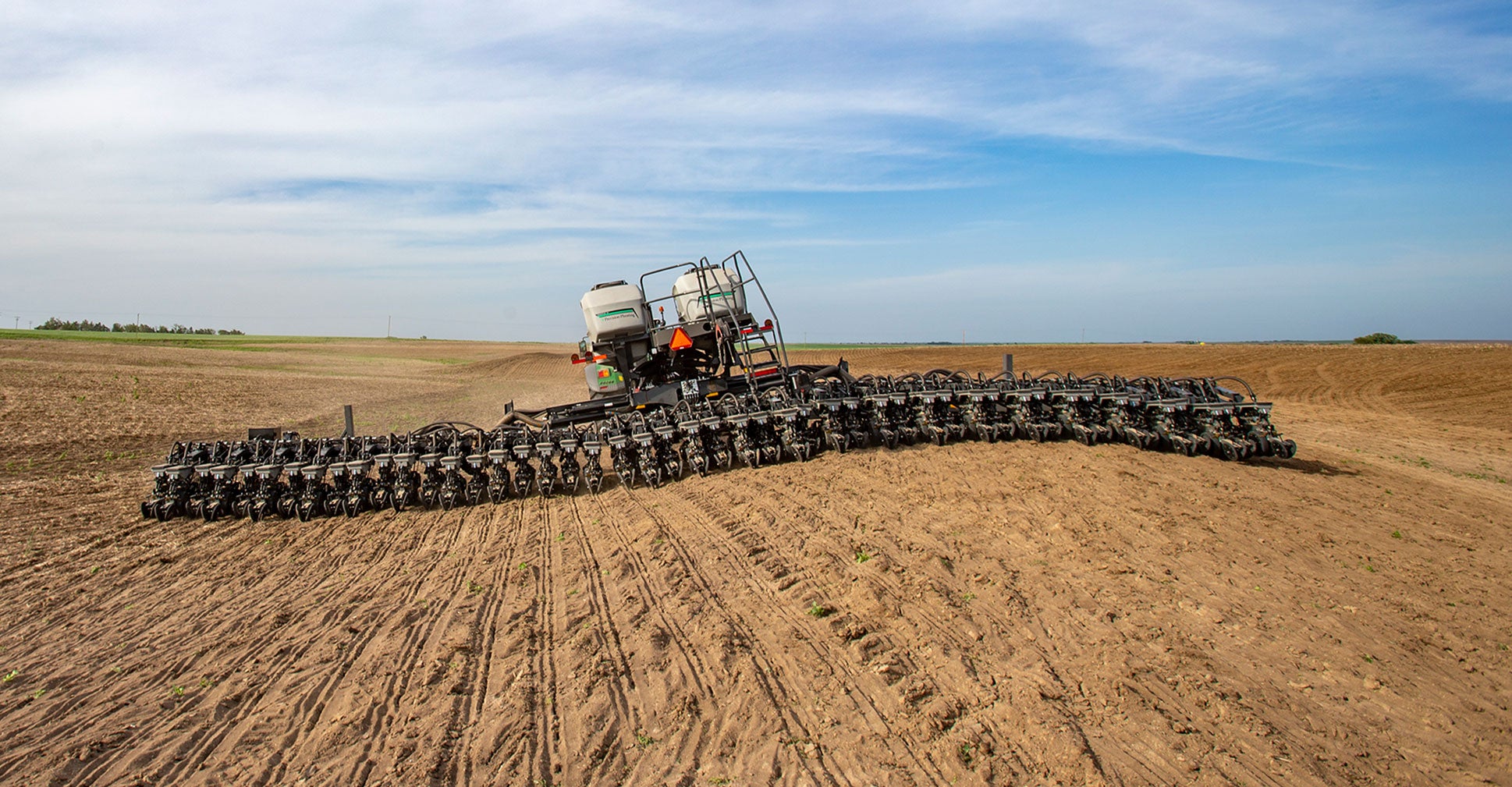
The problem of soil compaction becomes exacerbated by the use of larger and heavier tractors and planters. The damage from the planter’s tires as they travel across the field is especially detrimental to the soil structure. It is identified as pinch-row compaction.
Pinch row compaction is the space on either side of a row of corn in which a wheel of a tractor, planter, or some implement travels after the seed is placed in the ground. This compaction creates challenging conditions for germination, emergence, and root exploration.
Pinch-row compaction is specific to today’s large center-fill planters. The “pinch rows” are the center six rows. This means that 25 percent of the rows are pinch rows. On a 12-row center-fill planter, 50 percent are pinch rows.
2: Herbicide Applied Only to Weeds
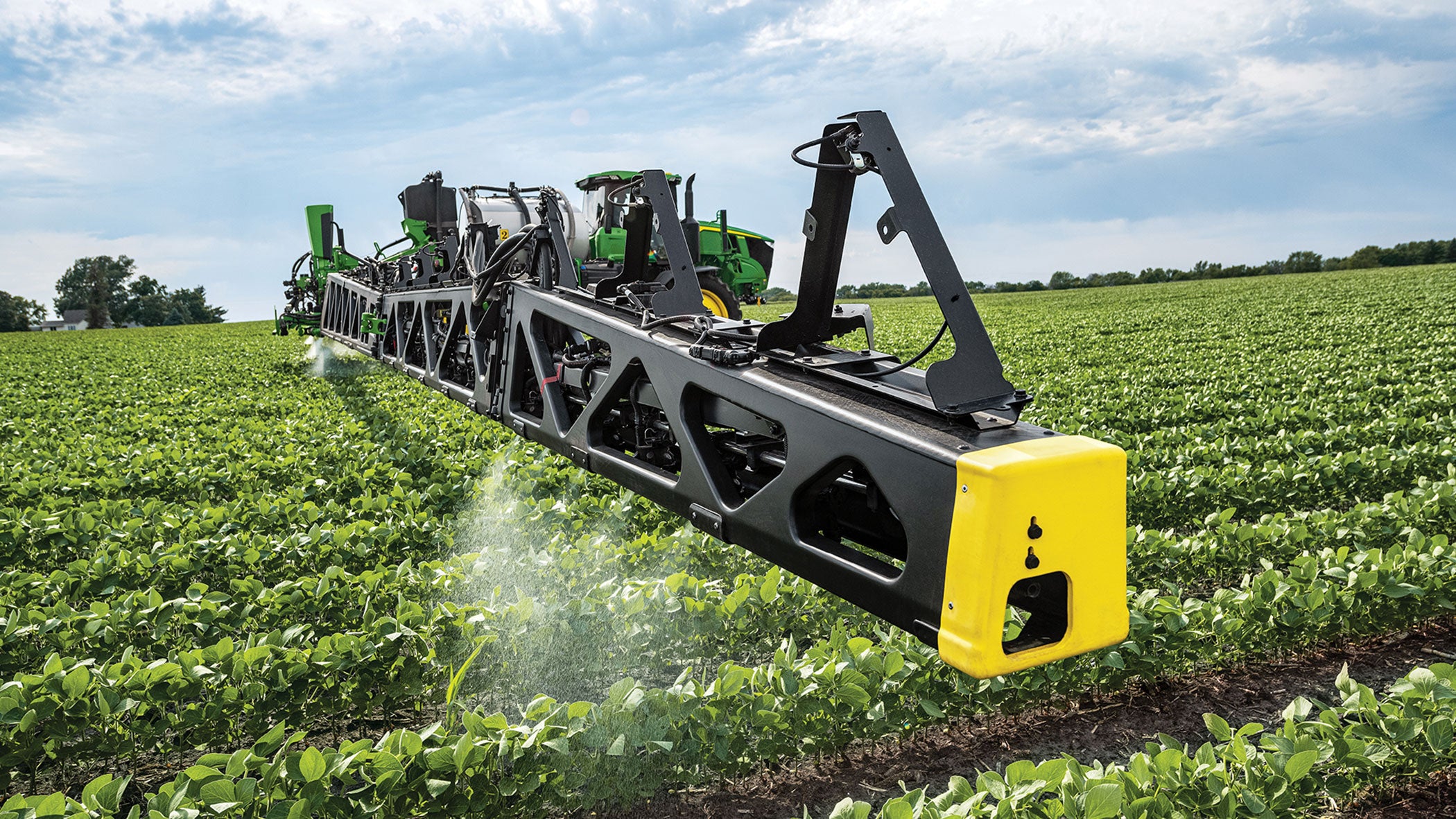
Anyone who has ever sprayed a field knows herbicide is often applied where it is not required. This wastes expensive chemicals and, over time, has the potential for a negative environmental impact.
The John Deere See and Spray system eliminates that by employing application-specific cameras to look for and identify where the weeds are. At 15 mph, the cameras update 20 times per second and instantly reference a database of over 1 million images.
Through its machine learning function, the system decides what plant needs to be sprayed and what herbicide to use from its dual tanks.
3: Improving Seed-to-Soil Contact
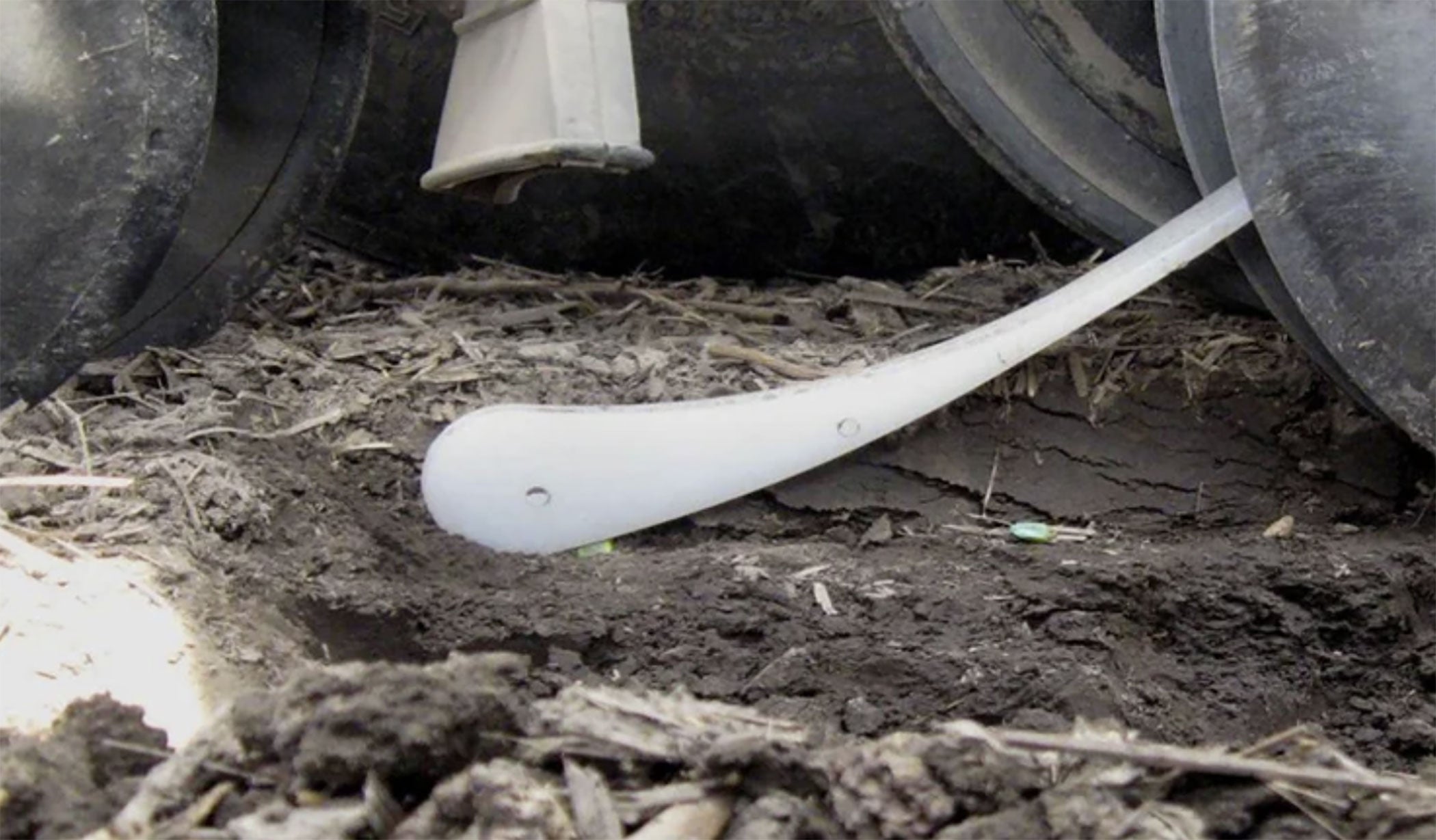
Seed-to-soil contact is essential for quick germination. Modern planters do an excellent job creating the seed trench; efficient closing wheels fill the furrow. But the seed may be placed in the trench with limited contact with the floor below it. This air pocket impacts the corn plant’s entire life and yield potential.
Recognizing this, the Keeton Seed Firmer was developed. It is an ingeniously simple and inexpensive device that attaches to each planter row unit. Once the seed has been placed, the Seed Firmer gently presses on it. This eliminates air pockets and assures seed-to-soil contact.
4: Minimizing Soil Compaction from Center Pivot Irrigation
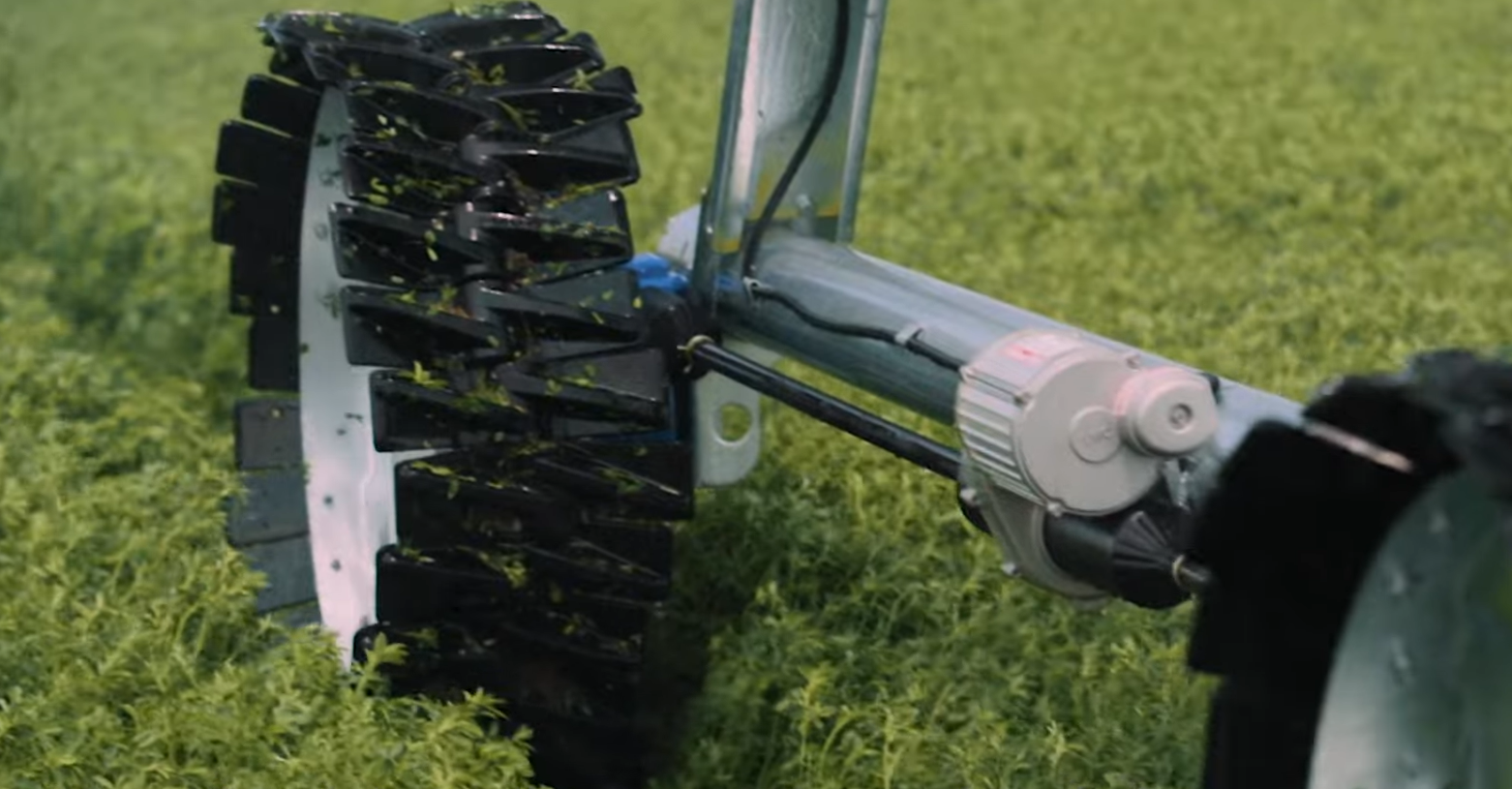
With the introduction of the Shark Wheel, the old saying there is no need to reinvent the wheel can finally be put out to pasture! The airless, high-traction, DNA helix-shaped Shark Wheel eliminates flat tires and minimizes soil compaction as it travels through an irrigated field.
Whereas a standard pneumatic tire on a center pivot system can create a trench nine inches deep or more, the Shark Wheel leaves a footprint of only around two inches.
This design is so soil-friendly that crops will often be seen growing back in its path. And the Shark Wheel is built with replaceable paddles that can be changed in less than 60 seconds if one gets damaged.
5: The Plant’s Real-time Requirement of Foliar Applications
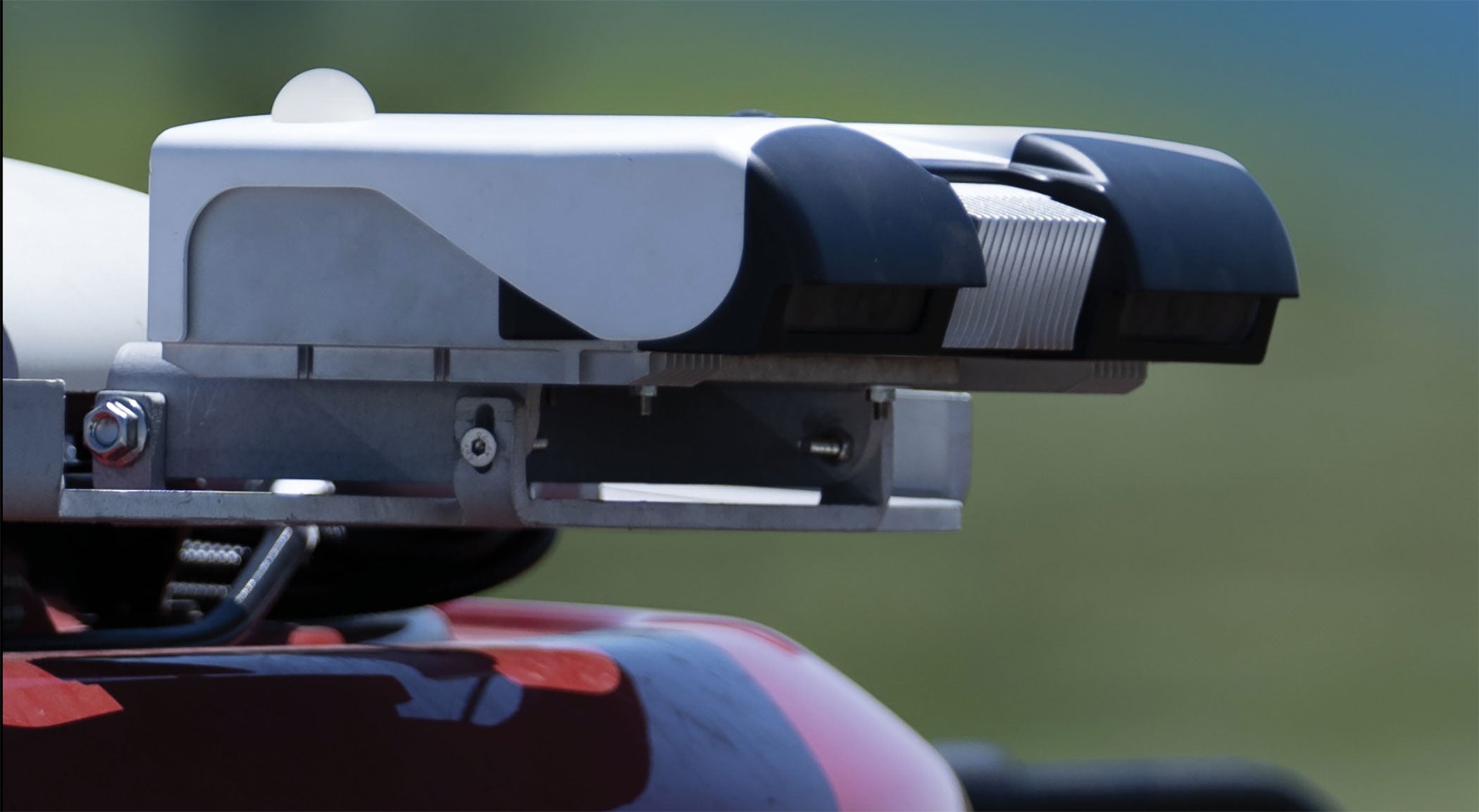
Preside-dress soil sampling, along with either tissue or sap testing, are all excellent to employ before any foliar feeding of your crop is done. The only issue with those procedures is that the sample needs to be sent to a lab; at best, the results may take a week or more to receive.
The data provided is accurate … for when the sample was taken and not for the day you want to foliar feed. It is an agronomic version of reading last week’s newspaper.
What if you could equip your sprayer with real-time multispectral cameras that analyze the plant’s requirements 50 feet ahead and then apply the proper amount of required nutrients?
You give the plant exactly what it needs to yield the most while controlling your input costs. Sounds like something you could only wish for, until now.
6: Improving Harvest Efficiency
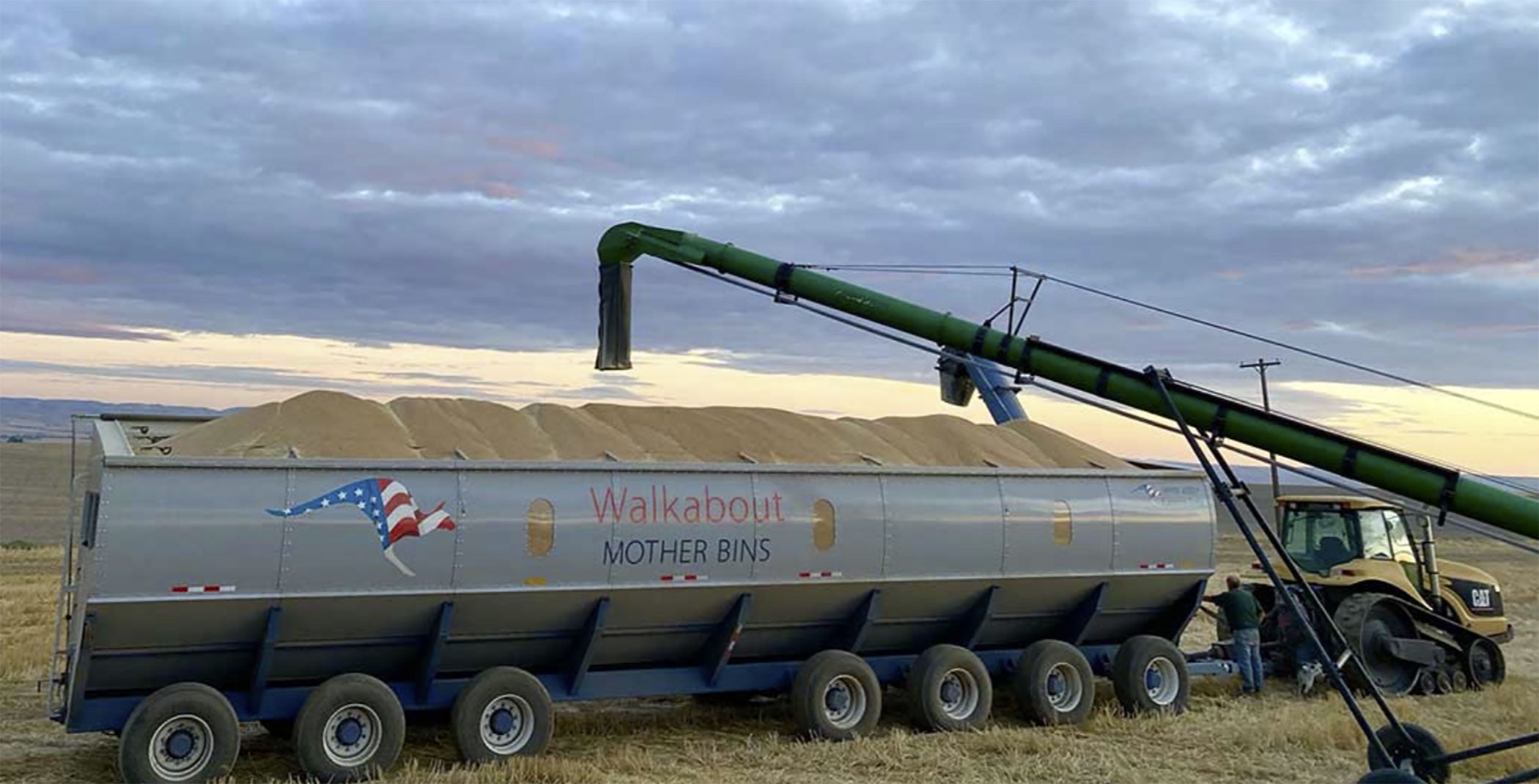
This movable system is called a Walkabout Mother Bin and is made here in the U.S. The in-field portable storage allows the grain cart or combine to empty into it. At the same time, a truck can load on the other side, letting the combine run continuously.
The Walkabout Mother Bin offers either 4,000- or 6,000-bushel portable, towable storage that can be placed on the edge of the field or the side of the road. It’s a cost-effective means to drastically improve your harvest efficiency.
7: Reducing Soil Compaction from Field Traffic
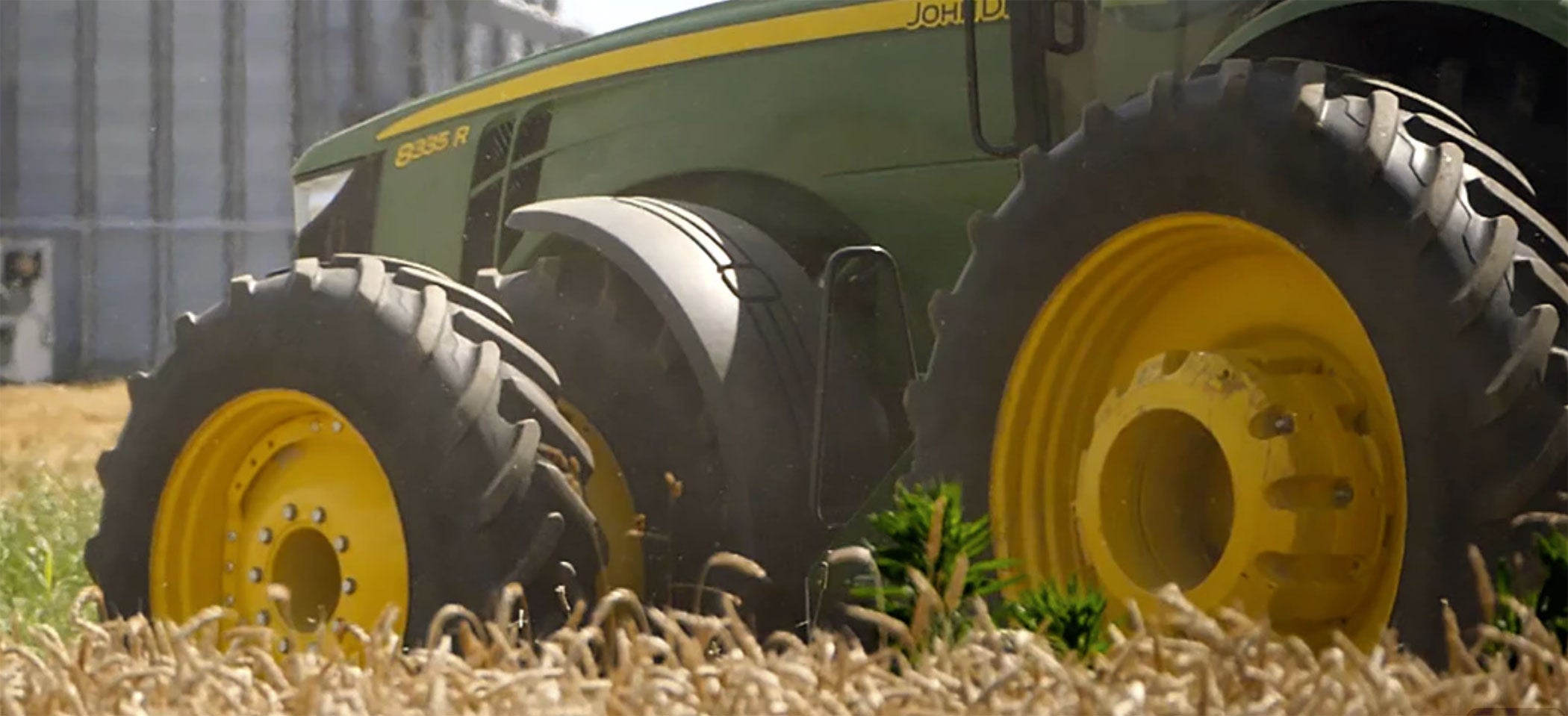
You must drive on the field with tractors, equipment, and trucks. Each time you do, the soil is damaged and compacted, resulting in less yield, poor water infiltration, and a lack of oxygen for the crops that grow in the traffic area.
Though the first pneumatic tires were a big step forward from steel wheels, other than radials, nothing much changed in the tire world.
That was until Michelin invented the IF and VF tire. Now, every major tire manufacturer offers these designs.
IF (increased flexion) identifies a tire design that can carry 20 percent more weight than a traditional tire at the same pressure. VF (very high flexion) tires offer 40 percent more load capacity at the air pressure of a standard tire.
Tire air pressure impacts not only the weight the tire can support but also the soil compaction. The higher the tire pressure, the greater the compaction. Thus, IF and VF tires allow the farmer to use 20 or 40 percent less tire pressure, respectively, than a conventional agricultural tire if no more weight capacity is required.
IF and VF tires trick your soil into thinking that substantially less weight is being applied to the ground than actually is occurring.