Through the flowering vineyards of France, a glimpse of farming’s electrified future sparkles in the distance. And it’s not just the wine that has people excited. The American farmer’s race to the bottom line may ultimately be won on strips of lithium, as improvements in electric farm tractors promise to someday leave traditional fuels and their associated costs in a cloud of smoke. While the reality of a fully-electric commercial farm operation is still spoken of in the future tense, its reality is becoming more present as improved costs line up with environmental considerations.
Today, European farmers work narrow fields using T4E electric high-clearance tractors, not unlike those their American counterparts use to spray pesticides. The 110hp electric saddle tractor features two power take-offs and can pull attachments used in working narrow vineyards and other similar settings. Manufactured by French Kremer Energie as part of an ongoing series launched in 2008, the T4E utilizes lithium ion batteries also manufactured in France by E4V that can be recharged overnight in about eight hours. The system typically works for 3,000 cycles, with each cycle being estimated at one day’s usage, costing French farmers on average 10 Euros a day ($11.16 USD).
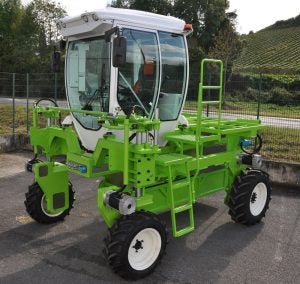
Meanwhile, American industry is likewise advancing along the same ideas, and a new white paper titled “U.S. Heavy-Duty Vehicle High Efficiency and Technology Suppliers” released by CALSTART — a member-supported organization representing more than 140 firms supporting high-tech, clean technology — suggests it’s a sector poised for growth. According to the research project’s scan of U.S. high-efficiency technology supplier sectors, about 80 percent of the country is already impacted by more than 255 companies operating in 535 facilities across 40 states, and the market is ready for more.
According to an interview with OEM Off-Highway’s publication for professional engineers, David Johnson, CEO of Achates Power, said the industry is gearing up to meet the interest across all fields.
“This report showcases what we know from experience: the U.S. is a leader in transportation tech, including next-generation advanced engines. Our industry can meet aggressive efficiency targets at affordable prices. Strong standards will encourage continued investment and drive advanced tech innovation and jobs in this sector.”
John Deere’s initial foray into the field in 2008 is often credited as one of the first American moves in advancing electric-powered farm equipment, although first introduced in Germany. The 7030E Series made its debut at the 2008 Agritechnica. The built-in power generator produces both 400-volt, 3-phae power and 230-volt DC power on-the-go, giving some to wonder at what point hydraulics will disappear from the power take-off completely. As with any emerging technology, the question of support arises, as implement manufacturers can’t produce the appropriate equipment until the base machines exist to work with them. But the first complementary unit born to match the 7030E Series was in fact a twin-disc fertilizer spreader utilizing three-phase power to drive the spreader motors in conjunct with 12-volt power driving the agitators and two electric actuators. The benefit to electricity is that drive speeds are controlled independently of the tractor engine’s revolutions-per-minute, and the equipment shuts down with the speed of a switch without the muss and fuss of hydraulics.
The Agricultural Industry Electronics Foundation, an international coalition of stakeholders vested in advancing electrical systems in the field of farming, presently has 11 project teams working on the development of electrical systems for such purposes as varied as conformance testing and ISOBUS automation, the universal protocol for electronic communication between implements, tractors and computers. One of the best-known challenges facing American farmers by way of electric machines, tractors and combines in particular, is the present limitations in speed for travel on public roads. One move Kremer has taken to address this is the utilization of reserve embedded energy. Another concern most farmers have is the present limitations in overall battery technology, making for challenges in the hot summer fields and cold winter barn-lots of America. High-temperature power electronics are being worked on at present as well.
Ryan Popple, CEO of Proterra, Inc., a manufacturer of zero-emission battery-electric buses, noted that the consumer demand across all fields will help propel all areas of the technology going forward.
“The U.S. is in the midst of a complete reinvention of how we transport people and cargo and, as demonstrated by this report, the U.S. in general, and California specifically, is at the center of electric heavy-duty vehicle innovation to make this happen.”
Among those new technologies hoped to address those present concerns is the recent development of lithium sulphur batteries, believed to represent the next evolution up from lithium ion batteries. Since Sony first commercialized the lithium-ion battery in 1991, it’s been recognized as the best material for storing the largest amount of energy at the highest density safely while allowing ions to flow in a graduated release and, most importantly, then be recharged. But now lithium sulphur batteries, such as those being developed by Sion Power in Arizona, are reporting their product can provide double the energy density of existing lithium ion batteries. According to Sion Power, sulphur ions pack five times the level of energy availability compared to other lithium formulations, and its present stated goal is to achieve a 500-watt hour per kilogram performance by 2018.
With battery technology improving at the speed of technology alongside the concurrent advancements in diesel-electric motors, the likelihood of American farmers being able to significantly cut fuel costs in exchange for cleaner vehicles seems as strong as the DC current in a new tractor.