“Factory” farming.
It’s a term I really don’t like. To me, the word “factory” implies an impersonal connection, or maybe a blank faceless corporation. And, of course, that’s what activists who are against large farms want people to think. But the reality is that 98 percent of farms — including the large farms — are owned by families who really put a lot of science and care into livestock production. Just because a farm is big doesn’t mean it’s bad. Any farm can do a great job regardless of size or label.
I tend to write about this topic a lot because I feel transparency and education are a huge part of understanding what happens on large-scale farms. But who helps these large farms? What sort of equipment and technology are used to treat livestock with the best care, and what sort of research is done?
To find out, I was beyond excited to learn directly from the experts themselves. Cumberland Poultry (a worldwide brand of AGCO Corp.) and I went to Auburn University and toured the National Poultry Technology Center, where they taught me about their research. Cumberland is one of the suppliers of equipment, which includes feeding systems, waterers, ventilation and climate control, lighting, controls, and alarms.
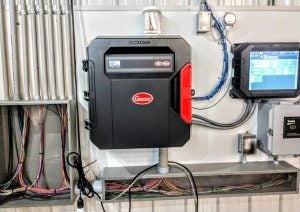
A typical chicken barn is about 66 feet wide by 500 or 600 feet long and houses around 30,000 birds. Separate breeder houses have hens that lay eggs where they’re incubated and hatch after about 21 days — and the first few days are absolutely crucial to ensure the chicks are off to a good start.
Chickens go to market between the ages of 32 and 63 days, depending on the size of the bird. Some companies may want a smaller 3.5-pound bird, whereas others may want them closer to 9 pounds; it all depends on the consumer product they are producing. But uniformity is critically key, especially for places such as McDonald’s, Chik-fil-A, and KFC. Environmental consistency is serious science!
In modern broiler (meat chicken) houses, the smallest difference can make a huge impact on the rate of gain. The more comfortable they are — and the more uniform the genetics and feed is — the better the overall business. One barn can cost a chicken farmer around $400,000, so every little bit of cost savings or health improvement really matters. Many farms are turning to solar power, changing their lights over to LEDs, harvesting rainwater, or utilizing fans to circulate air to ensure the chickens are comfortable at all times.
This video, done with the help of Kelly Griggs at the research center, shows us how it’s done:
This is where part of Cumberland’s technology comes in. In the video, Kelly shows the operation of a radiant heater that is used to heat the floor. She shows a portion of the heat (which we know rises) with smoke tracing that stays on the ceiling. Cumberland’s stir fans are used to push the heat to the floor where it can be used by the baby chicks. They also monitor and maintain the systems and teach this to their students.
The hands-on classroom setting here at Auburn University consists of around 60 students in a class, which is sometimes broken into groups where they learn all different parts of poultry housing management.
But what fun would a commercial poultry and livestock housing course be if you didn’t get to be up close and personal with the chickens?
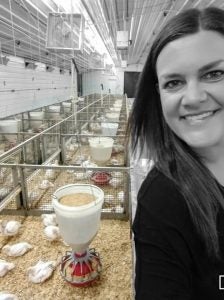
Here, poultry science students check the birds a minimum of three times a day to monitor health, feed, and nutrition plans, water and pressure, humidity, temperature, lighting, and more. They also gain skills in building structures, antibiotic research, backup generators — pretty much anything a biosystems engineering or poultry science graduate needs to gain employment in the real world. They even have an on-campus feed mill where they go through 24,000 pounds of feed per day for Auburn and other local research facilities. It’s a fascinating business! Shout out to Dr Jeremiah Davis who heads the National Poultry Technology Center, along with Kelly Griggs and Gary Sadler from Cumberland for the amazing day-long educational crash course, I learned so much! I encourage people to consider degrees or employment in this fascinating field. Here are a couple more photos from the tour:
Why raise commercial chickens this way? Well if you’ve ever had a backyard chicken flock, you probably know how easy it can be to lose chickens to predators, disease, weather elements, sickness, etc. Over the decades, these modern broiler facilities have continued — and will continue — to improve every year. This is how a lot of chicken programs ensure “no antibiotics ever” welfare standards and improve profitability and health, and reduce chicken mortality and sickness, among other positive steps. Science has improved every aspect of our lives, and chicken production is no different! To learn more, check out Auburn’s poultry engineering program at poultryhouse.com or Cumberland’s website at cumberlandpoultry.com.
Michelle Miller, the Farm Babe, is an Iowa-based farmer, public speaker, and writer, who lives and works with her boyfriend on their farm, which consists of row crops, beef cattle, and sheep. She believes education is key in bridging the gap between farmers and consumers.