Hay barracks, first introduced by the Dutch who immigrated to America in the 17th century, were open-sided structures with wooden posts and thatched roofs that could be raised or lowered to protect harvested hay. Farmers used the barracks to preserve hay and grain for their milk cows during winter when grazing wasn’t possible. Another method to store feed was to partially bury and expose wood-lined pits, which were referred to as silos.
However, because of spoilage from air exposure, these methods were eventually abandoned, and in the 1880s, silos evolved into above-ground, octagonal wooden structures treated in creosote. These were later abandoned in favor of stone silos, followed by mass-produced stave silos.
Many could argue that this sector is craving innovation and a fresh approach.
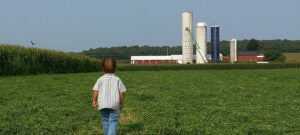
Today, four types of silos are generally used for storage: concrete stave silos, low-oxygen tower silos, bunker silos, and bag silos.
- Concrete stave silos are cylindrical and typically tubular shaped and can vary in size and diameter. Made of pre-cast concrete blocks that interlock together to create a high-strength shell, these silos are open at the top for loading and unloading. However, these silos can cause oxidation and dry matter loss.
- Low-oxygen tower silos are designed to keep contents in a consistent, low-oxygen environment to help prevent decay. These silos use large impermeable breather bags to keep air from getting into the silo through breather openings. During the warmth of the day, as the silo is heated by the sun, the gas trapped inside the silo expands. The bags will “breathe out” and then collapse. At night, as the silo cools, the air inside contracts, and the bags “breathe in” and expand again.
- Bunker silos (or pile silos) are structures where forage is filled and packed with front-end loaders. The filled bunker is then covered with a plastic tarp, typically held down by discarded tires. With these silos, the feed that is retrieved first is usually the last that was loaded in, which means there is considerable dry matter loss and potential for runoff from feed rot.
- Bag silos are single-use plastic tubes that vary in length and are packed using a blower, powered by a tractor, and sealed on each end once they are filled. They are unloaded using a tractor and front-end loader. The last forage taken out of a bag was the first retrieved. Bag silos can be more than 100 feet long, taking up valuable farming land, and can be torn by birds and other animals, causing the forage to be damaged.
As a result of the current state of these standard silo technologies, it’s predicted that U.S. farmers lose a total of $3 billion worth of forage during fermentation annually, not counting additional harvest or feed-out losses.
But Marvin Reiff, owner of Wisconsin-based Greenwood Silo and past president of the International Silo Association, is on a mission to transform the way the way feed and forage are stored through a combination of methods and innovations.
“When I first began working with Harvestore low-oxygen tower silos, I thought they were a joke, but the more I spoke to farmers and heard their criticisms,” Reiff said. “Then I began to realize the possibilities of sealed vertical-storage bottom-unloading storage systems. I knew there was something to the first-in/first-out feeding system in the preservation of expensive crops.”
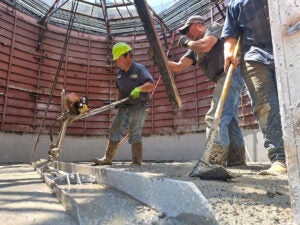
Growing up on a dairy farm, Reiff first started working with silos in 2006 after a relative asked him to dismantle and reassemble a Harvestore low-oxygen tower silo. From there, Reiff built a now-nationwide business maintaining and re-engineering silo machinery, transforming the functionality and efficiency of silos themselves.
After years of working with different silos, Reiff saw some areas for improvement, such as the high maintenance of silos, the slow unloading time, and being able to properly seal and maintain a low-oxygen environment with forage preserved at a moisture level below 50 percent to prevent dry matter loss. His aversion to low-oxygen tower silos is because they can be cumbersome in the time it takes for unloading as well as the climb to fill them.
Greenwood Silo’s innovations in alleviating silo maintenance have been considerable. Some of these include:
- A conversion that features a tapered and beveled stainless steel trough design with high-quality Samson chisel-tip hooks, which can double the capacity of the unloader.
- A variable speed frequency drive system that, with high-torque soft-start functions, that lessens the wear and tear, which helps avoid mechanical failures and broken chains.
- A side filling system to eliminate the need to climb a silo to fill it. With a heavy duty, stainless steel goose neck, a silo can be filled without climbing in a series of eight steps.
- A proprietary alert system to warn when a silo is within a few feet of being full.
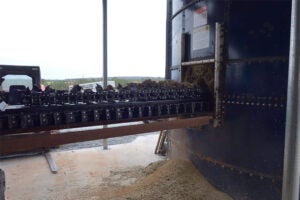
Reiff said he found that better forage is maintained by controlling the environment inside the silo and controlling the forage that goes into the silo. He came up with an innovative gas-trapping system to keep carbon dioxide from escaping and prevent oxygen infiltration while unloading. On his products, each of the bolts connecting the silo’s overlapping panels are sealed with an epoxy-like sealant before the silo is then pressure tested.
He also stressed that proper moisture control and field drying of the forage prior to going in the silo has been key in controlling moisture, which leads to fermentation. Reiff said he has found that harvesting and measuring the moisture level to below 50 percent helps ensure that feed remains rich with sugars, producing better nutritional feed for livestock.
Reiff developed his flagship silo after almost two decades of refining his methods and creating new tools. The new-hybrid monolithic silo is called The Greenline, a pre-cast concrete vertical storage system. He said his innovation combines the best attributes of both low-oxygen towers and concrete stave silos.
“I started thinking about this new design about ten years ago,” Reiff said. “Went back to the drawing board and looked at all the past silo designs and looked at their attributes. We looked primarily at building costs and long-term maintenance when coming up with the design.”
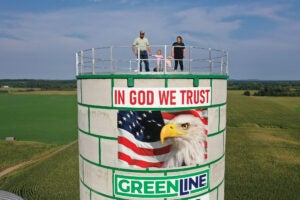
Utilizing many of the same techniques and tools he has learned throughout the years, Reiff completed his first pre-cast concrete vertical storage system silo in 2023 on the farm of Zach Janke in Humbird, Wisconsin.
The 25-by-124-foot silo combines the fast unloading features and stays cool because of its more than 6-inch pre-cast concrete walls. In addition, the new air-tight silo provides a more temperature-stable environment for feed.
The nutritional benefits of the new silos stored forage were verified in April when samplings of stored forage were sent to Dairyland Laboratories testing facility in Arcadia, Wisconsin.
Reed Dillon is a content brand specialist, marketing consultant, and freelance writer. He is the owner of Creative Brand Content in Moneta, Virginia.