Now that U.S. farmers are legally growing industrial hemp, the nation could see a rise in hempcrete construction.
Mechanical engineer Gregary Groeneveld picked up a 30-pound construction building block at Just BioFiber’s headquarters in Alberta, Canada. The block isn’t a traditional concrete cinder block. It’s made of fast-growing sustainable industrial hemp and looks like an oversized Lego.
Despite the historical social stigma of hemp, often thought to be the same as the psychoactive drug marijuana, industrial hemp won’t get you high. Hempcrete blocks used in construction don’t look or smell like a marijuana plant. They’re nearly odorless with a grayish earth-tone color.
In the U.S., most state officials define industrial hemp “as a variety of cannabis with a tetrahydrocannabinol (THC) concentration of not more than 0.3 percent.” Although industrial hemp has been legal to import into the U.S. since 1998, it has been illegal to cultivate commercially since 1957.
But that changed with the passing of the 2018 Farm Bill. The bill removed the designation of hemp as a Schedule I drug and reclassified it as an agricultural product, opening the market to American farmers once again.
For Canadian hempcrete manufacturing companies like Just BioFiber, sourcing locally grown industrial hemp is fairly easy since a supply chain already exists. Canadian farmers have legally cultivated industrial hemp for more than two decades and exported this cash crop to the U.S. since 1999.
Canada remains the single largest supplier of U.S. hemp imports, accounting for nearly 90 percent. But that could change. Now that U.S. farmers can legally grow industrial hemp, there may be a decrease in hemp imports and an increase in the local U.S. supply chain. In 2018, industrial hemp farming tripled. Montana farmers alone licensed the most acres of the crop at around 22,000 acres, with Colorado farmers in a close second with about 21,500 acres.
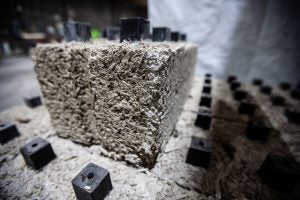
building system with carbon capture. (Image by Suzanne Downing)
Earlier this year, National Agricultural Statistics Service officials, under the U.S. Department of Agriculture, released the results of the 2021 Hemp Acreage and Production Survey in its National Hemp Report — noting the value of hemp production in the U.S. now totals about $824 million, including more than 54,000 acres of the crop being grown by U.S. farmers.
History of using industrial hemp to build and create
Using industrial hemp to make everyday items and build structures is nothing new. In the sixth century, people mixed hemp with clay to make wall plaster in the Ellora Caves in India, the Romans used industrial hemp to build bridges, Vikings used hemp fibers for caulking and fishing lines, early American settlers used it to make ropes and sails, and Thomas Jefferson penned the Declaration of Independence on hemp paper in 1776.
Industrial hemp has long been a desirable crop for farmers because they can grow it fast, it improves soil health, and it may reduce the need for some pesticides and fertilizers. Scholars report hemp was integral to many early European civilizations, and archaeologists uncovered a jar of hemp seeds in Germany that they believe to date back to about 500 BCE.
Benefits of using hempcrete
Since 2015, Just BioFiber in Airdrie, Alberta has been producing hempcrete building blocks for green builders. And U.S. interest in their blocks continues to rise.
Terry Radford described Just BioFiber’s hempcrete blocks as a green building block made from the natural insulating woody inner portion of a hemp plant stalk, known as the hurd. This hurd is broken into small pieces and separated from the fiber in a decortication plant.
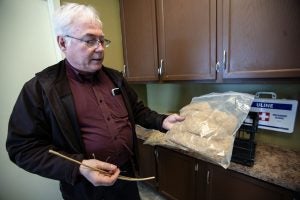
Just BioFiber sources giant bags of hemp hurds from a research farm and pilot facility in Vegreveille, Alberta. Then, they mix the hurd with a proprietary lime binder and press it into blocks using an assembly line machine. Each block has an innovative Lego-inspired structure built into the middle. That’s their claim to fame — the structural component.
“Hempcrete is often used as an insulation in frame construction,” Groeneveld said. “But with the interlocking block system we created, our blocks can actually be used for structural building.”
This Just BioFiber block is part of an entire interlocking wall system. Builders can cut each block to size during the building process.
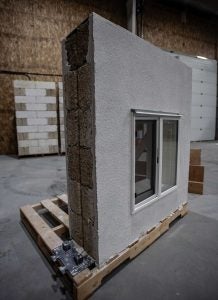
manufacturing facility. (Image by Suzanne Downing)
And these hempcrete blocks are also extremely good for the environment.
“Hempcrete actually removes carbon dioxide from the air while the biological plant fiber grows,” Radford said.
That’s because Just BioFiber’s engineers make these blocks using industrial hemp fibers that sequester 110 to 130 kg of CO2 per cubic meter, or 32 building blocks. By using this fiber, atmospheric CO2 is significantly reduced — making the blocks carbon negative.
There’s a myriad of benefits to using hempcrete blocks in construction other than sequestering CO2. They can be stacked up to five stories high. There is no mold, no pesticides, and no pests, and each block has a two-hour burn rating. The blocks filter particulates and create a barrier of thermal mass that helps regulate interior temperatures.
“It’s an advanced composite,” said Groeneveld, referring to the innovative Lego-like block center in each hempcrete block. The block, he explained, is a thermal set, so it’s not a normal plastic since it has glass fiber in it. And under high temperatures, it doesn’t melt like a normal plastic.
“It’s sort of like an egg. You can cook it but you can’t un-cook it,” he added.
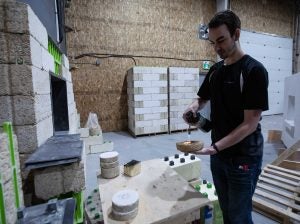
Groeneveld picked up a blow torch and directed the flames directly onto a small sample of hempcrete. It didn’t catch on fire, and after a few minutes it was barely warm to the touch. The official fire rating test Just BioFiber conducted during research and development lasted two hours. Engineers heated one side of the wall to 1,000 degrees Fahrenheit. After two hours, the other side of the hempcrete wall was only around 120 degrees.
Terry Radford’s brother, Mac, founded Just BioFiber in 2015 after years of inventing and fabricating hempcrete block prototypes out of his garage, and just three years later, builders completed construction on one of Just BioFiber’s biggest projects on Vancouver Island, known as the “Harmless Home.” It was the first of its kind with exterior walls made of hempcrete blocks.
Another Just BioFiber large-scale project is to supply hempcrete blocks for a 112,000 square foot “EcoLock” storage facility in downtown Kelowna, British Columbia. This five-floor facility will be the first of its kind in North America to combine storage and office functionality in an environmentally responsible building.
Just BioFiber, like other global hempcrete production companies, continues balancing local and global efforts to meet basic human needs without destroying the natural environment. That’s really the goal with their building blocks. To them, environmental justice is as important as sustainable development.
Hempcrete homes in the U.S.
In the U.S., there are only a handful of homes built with hempcrete. Builders completed the first hempcrete home in the U.S. in November, 2015 in North Carolina, using imported materials for the build.
But the nation could see more hempcrete homes popping up across the nation with the legalization of U.S. cultivation of industrial hemp. Not only will the supply chain grow stronger since builders can source local hemp, as the hempcrete construction infrastructure grows, there’s less risk to investors.
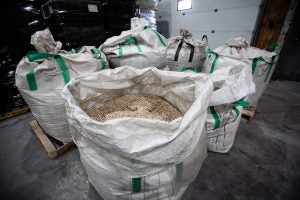
There are already a number of U.S. hempcrete suppliers established. Like Left Hand Hemp in Colorado, founded by Kelly Thornton, Hempitecture in Idaho, founded by Matthew Mead, and Hempire in California, founded by Sergiy Kovalenkov.
“I think we’ll begin to see hundreds of thousands of houses in the next 10 to 20 years in North America,” Kovalenkov said.
“Because of the Farm Bill, things have completely changed.” Before there was nothing for Kovalenkov to talk about with investors.
“Our hands were tied because it was not legal,” he said. But now, Kovalenkov is hopeful that as interest from farmers and potential processors grows, it will be easier as far as the supply chain.
“It will result in more biomass, and it’s a big plus for the industry overall,” Kovalenkov said.
Mead is also optimistic for the U.S. hempcrete industry despite Idaho being one of the states not following suit and keeping state law to prohibit the cultivation of hemp farming in the state.
“With the new bill, there’s a heightened collective awareness of hempcrete in the U.S.,” Mead said. “The challenge now is a lack of uniform construction codes.”

The same is true in Canadian suppliers like Just BioFiber. Radford said that although Just BioFiber’s hempcrete blocks are gaining interest in the United States, there are still hurdles facing construction.
“Hempcrete doesn’t have a ‘code book’ for engineers,” Radford said. “The hempcrete material and structural system is just gaining momentum, so it’s a learning curve for structural engineers. And in most cities, building with hempcrete is still not allowed.”
“You’ve got steel, concrete, and wood,” Radford said. “Those are your three structural building materials.”
And because Just BioFiber’s hempcrete is used for a combination of construction products (it’s a composite product and it’s the wall system, the insulation, the sheathing, the structure, the vapor barrier, the conduit), there is a lot involved in one material.
“You have to get more than one test and certification. It’s a whole system. It’s replacing a bunch of things,” he added.
Radford hopes to be at the point where Just BioFiber will have an actual building code certification.
“Then, the engineers won’t have to call us and get all of the information. They’ll be able to get it from the International Building Code or from the national building code.”
However, if a U.S. city won’t allow hempcrete construction because of municipal building codes, builders simply have to build elsewhere. But that is slowly changing.
Hempcrete builders such as Hempitecture and Tiny Hemp Houses offer services across the U.S. with hempcrete installation. Hempitecture founders believe, “Our homes should contribute to our health, not take away from it. They should help us live happier lives, while also doing no harm to our planet. Hempitecture is on a mission to create healthy, energy-efficient materials that positively impact both people and the planet by capturing carbon dioxide and replenishing farmland.”
The hempcrete construction industry continues to gain in popularity across the U.S. and Canada. Reducing carbon emissions continues to be at the forefront of America and an important aspect of modern agricultural practices. By using a carbon negative building material for residential construction, like hempcrete blocks, the hemp industry could be a lucrative industry once again as the local supply chain becomes secure.
As a result, the U.S. could see a rise in hempcrete homes. The stigma of industrial hemp cultivation is changing. And an ancient “green building” technology is making a comeback.
Suzanne Downing is an outdoor writer and photographer in Montana with an environmental science journalism background. Her work can be found in Outdoors Unlimited, Bugle Magazine, Missoulian, Byline Magazine, Communique, MTPR online, UM Native News, National Wildlife Federation campaigns and more.