GOODYEAR, Arizona — On a Christmas Eve some 75 years ago, five siblings in the Rayner family walked into the living room of a small house north of Estrella Mountain and found it stacked with presents like they had never seen before.
The surprise grew when, not long after, they moved to a newly built house with a front lawn.
“It wasn’t till later when I put the combination together: ‘Dad must have made some money,’ ” Ronald Rayner, 82, said with a grin, sitting in a modest office room about 100 feet away from the house where he grew up. It’s land that to this day, despite urban sprawl, he still farms with relatives.
Rayner witnessed the boom of cotton farming in Arizona at an early age. It was a time when 42 percent of the total cropland in the state was cotton most of the year, and miles of it bloomed from Yuma to Safford, when nearly 100 cotton gins — short for engines — ran without a break from October to February.
That time of plenty was short-lived. Prices fell and acreage dropped before the 1960s, then rose again in the 1980s. But never again was there so much cotton blooming in the state, and with slight ups and downs, the number of acres planted has fallen steadily. Today, Arizona growers plant as many acres of cotton as their relatives did in 1914, when there were no mechanical pickers, and when the crop was enshrined for its economic promise.
Yet cotton fields have been paved over across metro Phoenix, displacing most production to water-stressed Pinal County and forcing growers to find new ways of staying in the business.
Arizona cotton farmers grow more with less today; yields are five times higher than a century ago. Industry leaders and experts agree cotton acreage has not and will not expand in Arizona, but they see promise in growing contracts for seed, technological innovation and the potential for organic markets.
“While we’re not necessarily big, we’re still pretty mighty,” said Jadee Rohner, executive director of the Arizona Cotton Growers Association.
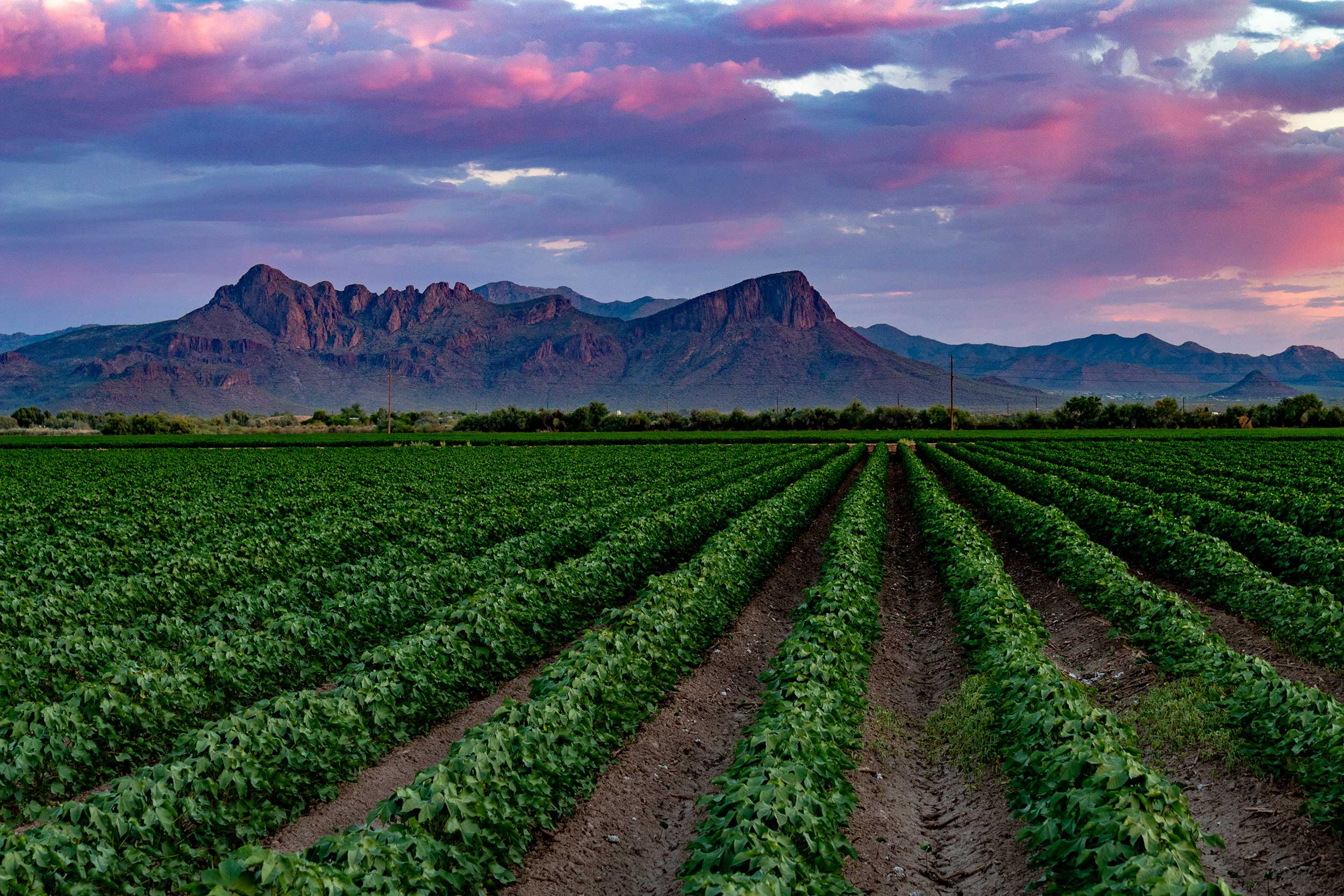
Arizona cotton growers rank among the top three nationwide for yield, and grow some of the highest quality Pima cotton, which has a longer and softer fiber than the more popular upland cotton.
Arizona growers also contract with company giants to produce the seed planted across the cotton belt, making Arizona “the greenhouse for cotton seed,” Rohner said. The premium price they get from selling seed, she added, makes up for the losses of a low market price for the fiber.
Companies are also investing more in sustainability and traceability programs so consumers have proof of where and how the fiber was grown. Rohner believes there will be a slow expansion toward organic cotton farming in Arizona.
About 30 percent of Yuma’s leafy-green farmland is certified organic and sits fallow in the summertime. Planting organic cotton could provide cover from erosion, improve soil health, and maximize operations’ profits, said Macey Keith, an extension worker and Ph.D. student running trials and surveys in the area. However, in many cases, that comes with a cost because of the added water resources often associated with growing cotton organically.
Only 1 percent of the cotton grown in the state is organic, but now there is infrastructure for that number to grow. The Chandler Ginning Company just got an organic certification for its Eloy gin and this year will process 1,800 bales of it in-state.
Central Arizona still blooms white every winter, even if it’s not the spectacle it once was. Across the state, 10 gins run after the harvest is over. Last year, they wrapped nearly 250,000 bales of natural fiber, which is sold to a world market and shipped overseas.
Arizona’s climate also comes with advantages. The state is free of Fusarium wilt, “the worst disease for cotton in the world,” said Jim Olvey, a prominent private cotton breeder from Arizona who has worked the past six years to find resistant varieties for other states. The disease had the potential to destroy the U.S. industry. Olvey thinks the spores couldn’t withstand the arid heat.
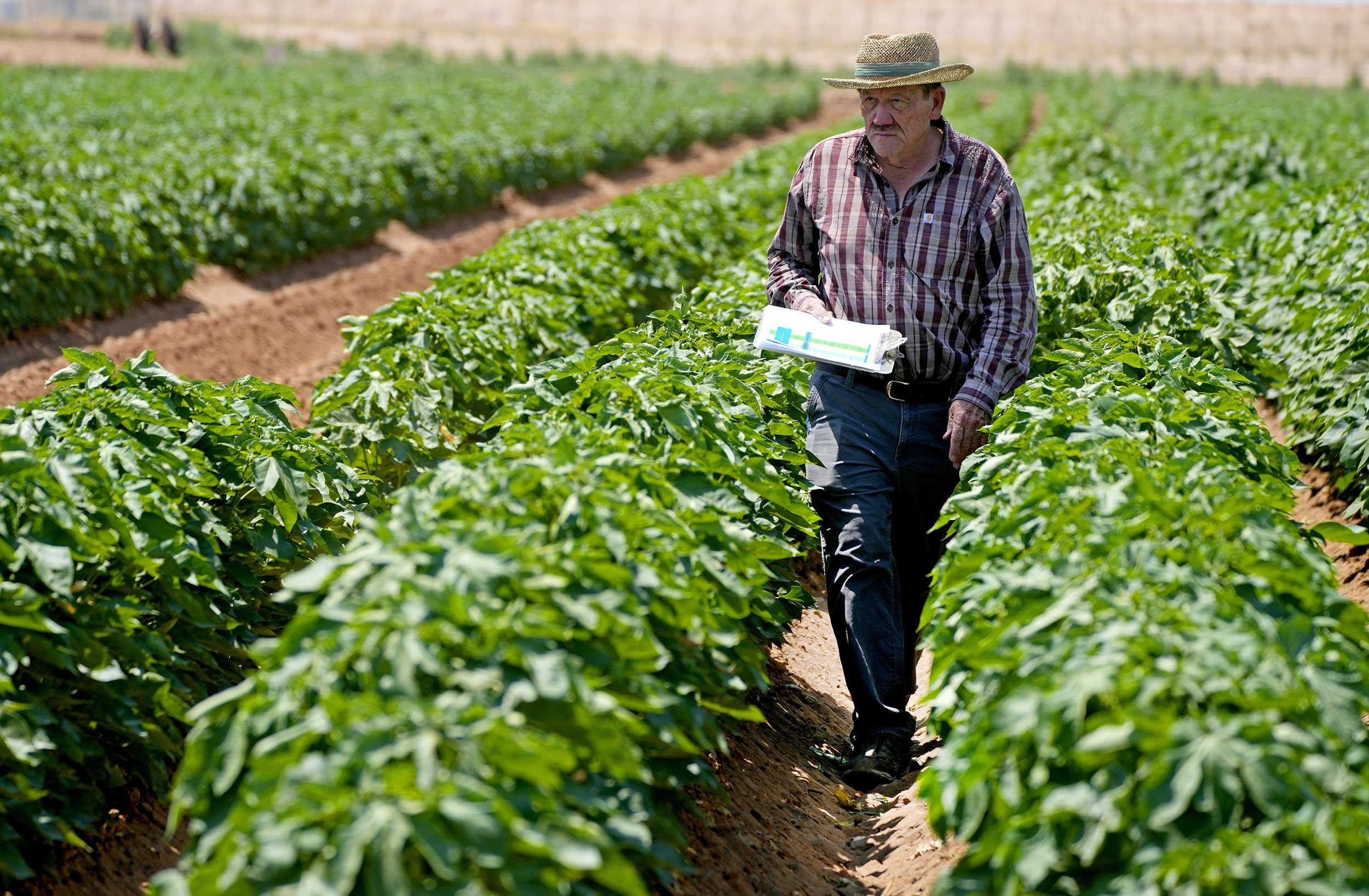
Advocates say no matter how many acres are lost, cotton will always grow in Arizona. It’s a desert with the right climate for the crop, nearly disaster- and disease-free conditions, with a lifeline and safety net of government subsidies, and a few committed farmers who, out of tradition or convenience, will remain cotton growers.
The cotton bust: Growth wins out
Rayner still owns land in west Phoenix with his brothers, nephews and son. At one point, the family operations spread over 10,000 acres in central Arizona, but they have shrunk to a dispersed 5,000 acres over the state, most of it leased. The role of cotton in “A Tumbling T Ranches” has changed much, as has farming overall.
The incentive in the 1950s was obvious: The crop was extremely profitable. Wartime industrial expansion enriched the U.S. and, in the strengthened economy, consumers were hungry for goods that made manufacturing grow. Cotton gins and mills expanded. Cropland in Goodyear, built half a century before to supply the demand for airplane tires during World War I, had its comeback.
By 1954, Arizona had the highest cotton production in its history, and half of it came from Maricopa County. A few decades later, buildings and warehouses replaced farmland at a startling pace. Growers in the county now contribute a meager 6% to the state’s cotton production.
Incentives to grow cotton today are not straightforward. Tradition, expensive equipment investments, ongoing seed contracts and establishing a rotation between crops are in the mix.
The decision to plant an eight- to nine-month crop like cotton is also a big risk. In many areas, farmers don’t know ahead of time how much water they’ll have for the season or if the landowner will break the lease on short notice.
“You can see the writing on the wall,” said Ross, Ron Rayner’s son, a managing partner who oversees the company’s land assets. Next to the office, by Litchfield Road, a wheat field they harvested in the late spring of 2023 was paved and built into a Microsoft warehouse months later. The family decided to buy land in Buckeye after being surrounded by Goodyear.
“There’s not going to be much left in this area for very long.”
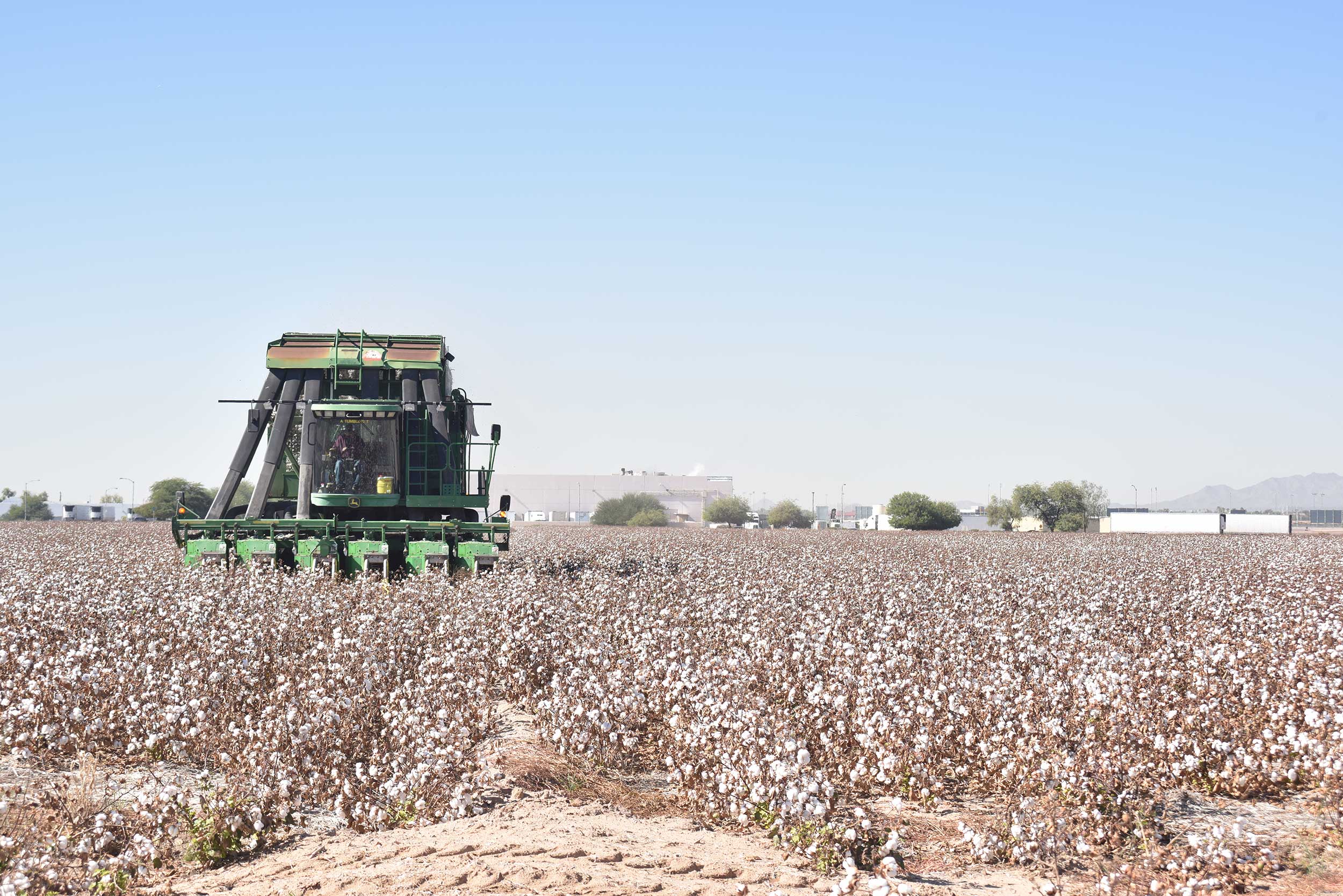
Pinal County took the lead in cotton production but it’s likely to run a short term. Development is having its boom there as the county grows at a rate faster than anywhere else in Arizona, and lawmakers are seeking ways to make farmland water salable to cities. After losing virtually all Colorado River water for farming, growers are forced to use dwindling groundwater supplies.
Nancy Caywood’s family in Casa Grande saw the boom and bust of cotton farming twice. They’ve survived it and kept cotton close to their family. But every year, they are unsure if they can plant. Low water levels in the San Carlos reservoir, high payments to the irrigation district and low gains from poor market prices put their farming operation at risk. Caywood’s son, a firefighter, leases land elsewhere to grow alfalfa just to keep the family farm.
“Everything is year-to-year, season-to-season,” Caywood said.
Last year there was a huge increase in planting across the state, with 32% more upland cotton than the year before. But it wasn’t because the cotton prices were better; prices for other summer crops, like corn, were worse, said Rohner, with the Cotton Growers Association.
Most years, Caywood plants no cotton. Five years ago, the farm only had 100 acres of it. But looking at the crop field makes her feel good with a sense of pride, so she became an advocate and educator. For decades she has received tourists on the farm. She talks about farm life, machinery and the long list of products containing cotton or cottonseed, like dollar bills, blue jeans, airplane wings, popcorn, rocket propellants, book bindings, nail polish, X-ray film and Twinkies.
She also plants a small plot of cotton and keeps the crop up until mid- or late March, way past harvest time, until the lint hangs from sticks like a torn-up pillow, giving visitors a souvenir to take home. A group of senior East-Coasters visiting in spring commented in awe: Who knew that you could grow cotton in the desert?
Farming cotton in the desert
Dennis Palmer started sneezing almost as soon as he stepped into the Safford Valley Cotton Growers gin. He is allergic to the lint and he said he could make more money if he had a different profession. But cotton farming is more than a job, he said.
Both his grandparents farmed cotton, one of them all his life, and he can see doing the same himself until he can’t.
“It’s personal,” said his son Matt Palmer, co-owner of VIP Farms. “We take pride in what we do and who we are.”
Tradition often comes first among the reasons farmers stick to cotton. Due to their generational history with the crop, they know how to do it well, and will call themselves “cotton growers” no matter how many other things they grow.
There’s a larger mix of things that also compel them to keep growing. Many own equipment and decide to plant just enough to keep their local gin running. The balance is fragile in counties with only one gin, like Yuma and Maricopa, where acreage has shrunk so much that costs hardly pencil out.
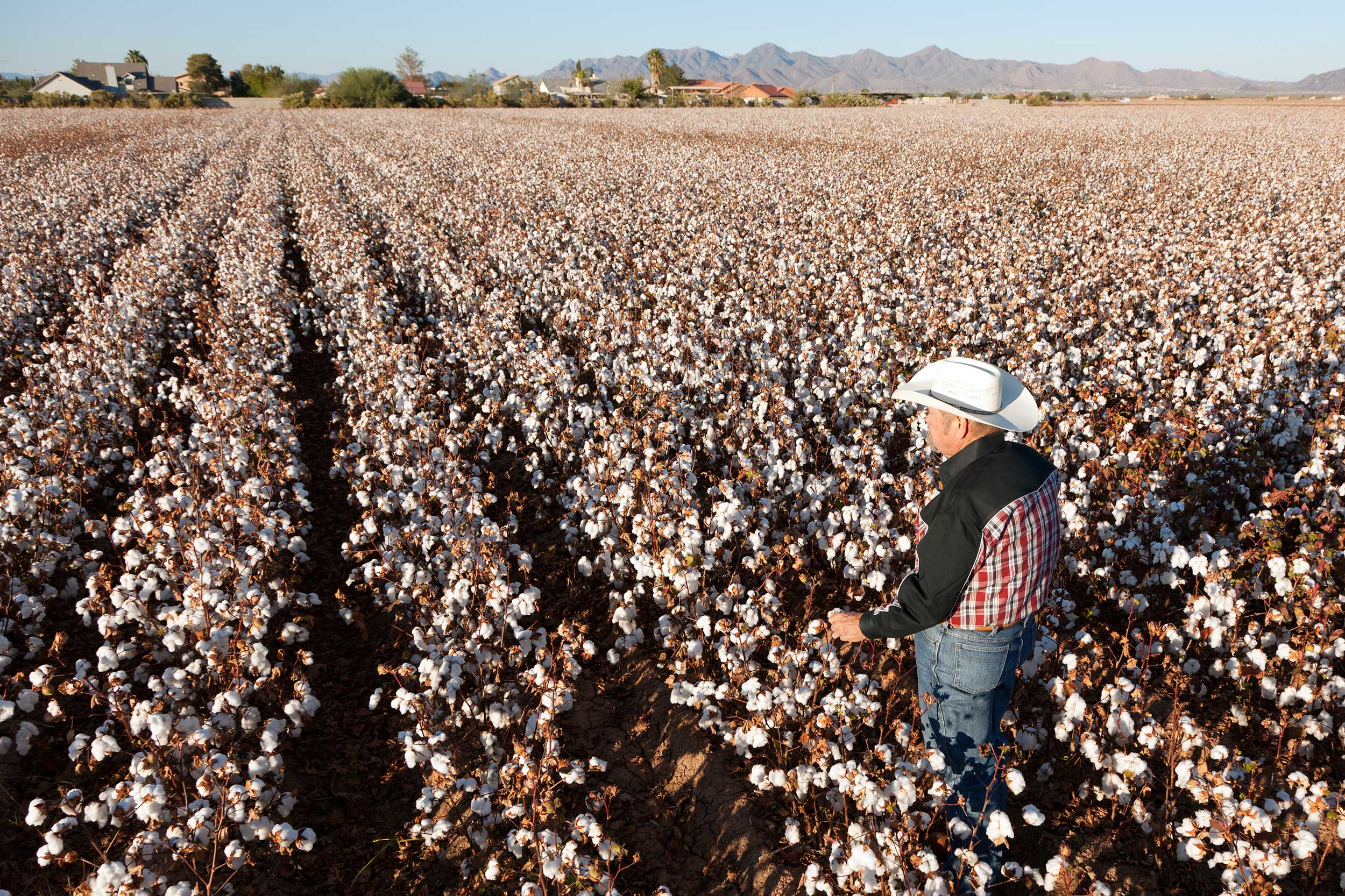
The Rayners are co-owners of the last active gin in Buckeye, which has only 12 members. In their time running, they’ve processed as much as 62,000 bales a year. In 2023, the output was about 5,000 bales.
“It was barely worth running the gin for,” Rayner said. Members often plant to make sure this valuable and expensive infrastructure is not lost for good.
George Frisvold, a specialist in agriculture and resource economics from the University of Arizona, sees signs of optimism in the future of the crop and believes the downward trend in cotton acreage will flatten out instead of crashing.
“Arizona cotton has found a niche,” he said. It’s one of the best places to grow drought- and heat-tolerant seeds that other states will plant.
Today, most cotton growers contract with seed companies to produce seed varieties for them. Giants like Bayer, BASF, Americot, and Corteva together hold 90% of the cotton seed market, according to Farm Action consolidation analysis.
The biggest advantage of the state product is the yield and the quality.
Arizona, for better or worse, doesn’t get the heavy rain other cotton belt states do. Excessive rain can severely damage the “grade” or quality of the white fiber and how much growers get paid for it. Arizona growers control irrigation, said Mike Olvey from American Pima Seed and O&A Enterprises: “We’re always going to make a crop.”
Cotton is mostly grown in Pinal, Graham, Yuma, Pima and Maricopa counties. The first two make 65% of all production. About 8 in 10 acres are upland cotton, and the rest is Pima, which has the highest-quality fiber but cannot withstand central Arizona’s extreme heat.
Arizonans are also better covered for planting cotton than other crops in the desert.
Insurance subsidies in the state are nine times higher for cotton than for the next highest subsidized crop, a ProPublica investigation found.
Government support for cotton growers goes back to when the fiber powered the young American nation, two centuries ago when mills mushroomed in the East and stood as a symbol of progress and independence from the British, and when the lobbying and political power of the industry were undisputed. Expanded support became key during farm crises like during the Great Depression and the 1980s.
“Congress stepped in and created emergency programs to keep the sector from collapsing. And over time, those programs became codified into the subsidy programs we have now,” said Karen Hansen-Kuhn, who leads trade policy research at the Institute for Agriculture and Trade Policy and has examined the impact of cotton dumping policies worldwide.
“There’s been some changes over the years in the structures of those subsidies,” Hansen-Kuhn said. “It’s certainly true that the most powerful sectors got the most amount.”
But if the U.S. is to produce any cotton, growers need these subsidies, said Palmer, the grower from Safford. This year, Bayer increased the cost of Pima seed by 25 percent for growers in Greenlee and Graham counties. The crop is also exposed to the elements and volatile market prices.
“All these costs are skyrocketing,” Palmer said. “And so, we need some kind of safety net in insurance programs.”
Insurance payments and crop subsidies avoid the necessity of spending on even larger disaster-assistance programs at taxpayers’ expense, former Agriculture Secretary Tom Vilsack told The Arizona Republic. In the last two decades, federally subsidized programs paid farmers about $55 billion to indemnify them for the effects of drought.
“There’s going to always be a need for public support to agriculture,” said Hansen-Kuhn, noting that the sector is unique and subject to many whims that are out of farmers’ hands. “The question is what kind of support we are providing.”
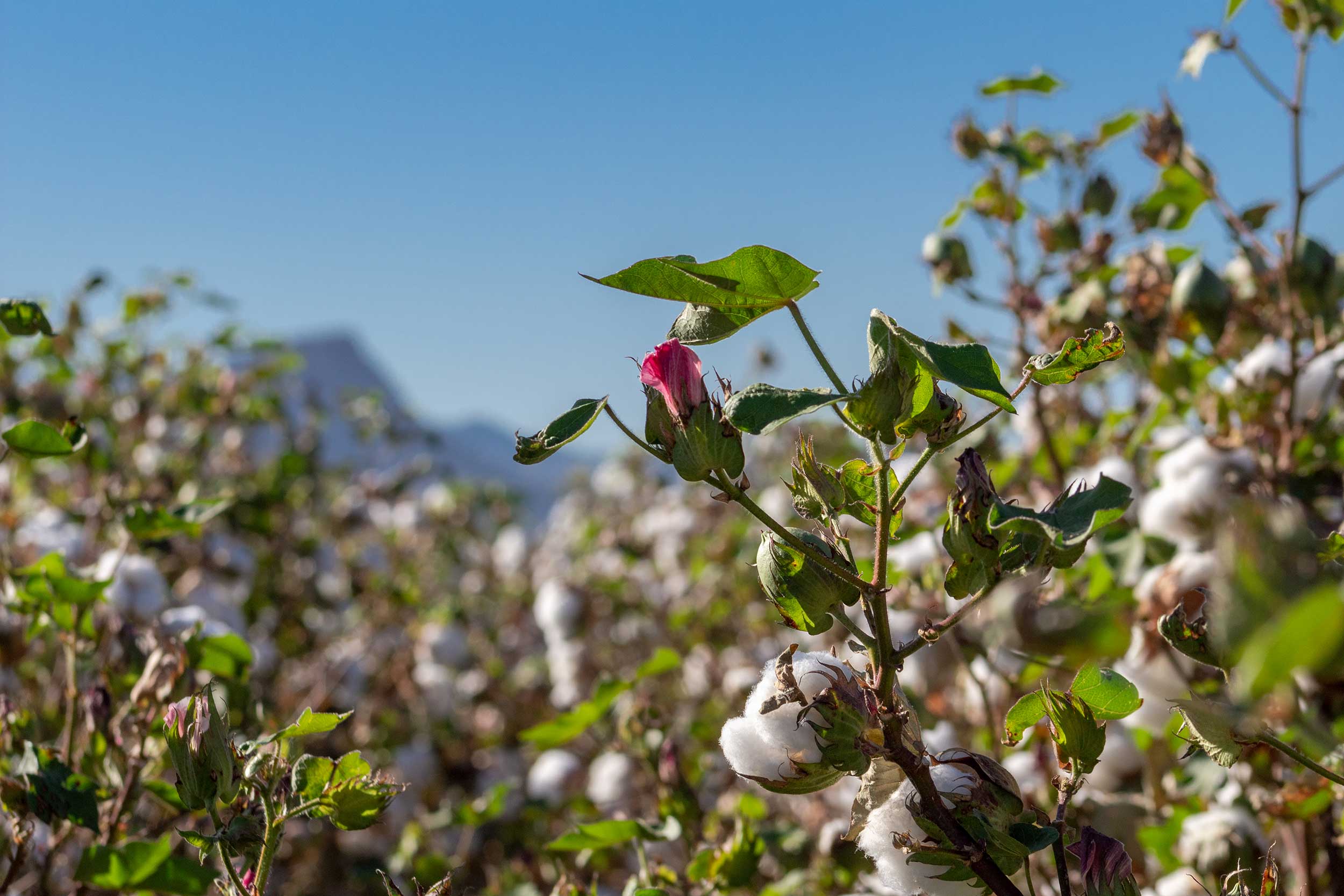
To maintain his profit margins, Palmer has grown. Decades ago, his grandfather farmed just 75 acres of cotton and did other things on the side to survive, “but here we are in the thousands of acres. And so that economy of scale just continues to get bigger,” Palmer said. “You have to work more acres to keep up with all of your investments, the cost of everything.”
VIP Farms, his business, is diligent in adopting the newest technology and practices. Soon after Matt, Palmer’s son, joined the business in 2000, they started using GPS technology and auto-steer machines, recording field data to be precise and efficient on fertilizer and insecticide use.
“It’s continual,” Matt Palmer said. “It’s hard to stay up to it all. But if you don’t, you’ll get behind the curve real quick.”
Even being competitive and having insurance coverage, they have to get lucky with the weather and market prices, Palmer said. “Sometimes you can just work yourself to death and things will go wrong.”
“But we’ve decided this is our life’s work. So by golly, we’re going to give it our best shot.”
Advancements in biotech
Cotton farming has made big strides in sustainability in the past decades. Known for being a chemical-intensive crop, cotton changed its face.
In the 1970s, cotton farming accounted for 25 percent of the pesticide use in the U.S., and Arizona growers would apply pesticides about eight times in a single season. Today, the average pesticide use is 0.5 times a year per farm, said Rohner — one application or none at all.
A long-snouted beetle and a rose-ringed caterpillar terrorized cotton growers for a century, and still do in many regions of the world. The first was named boll weevil (Anthonomus grandis) and eats and lays eggs on immature cotton bolls; the second was pink bollworm (Pectinophora gossypiella). The larval stage of this gray moth, native to Asia, hatches inside the cotton boll and preys on its lint and seeds.
After throwing arsenic on the ground from horse-pulled carts with their bare hands or blanketing the land with DDT via aircraft, cotton growers got access to new tools. Some are within the seed’s DNA through genetic engineering; others are based on savvy monitoring of pest populations and the introduction of other insects that prey on them.
The U.S. Department of Agriculture declared both pests “eradicated” in the U.S. in 2013 and 2018, although that doesn’t mean they couldn’t develop resistance again and devastate crops.
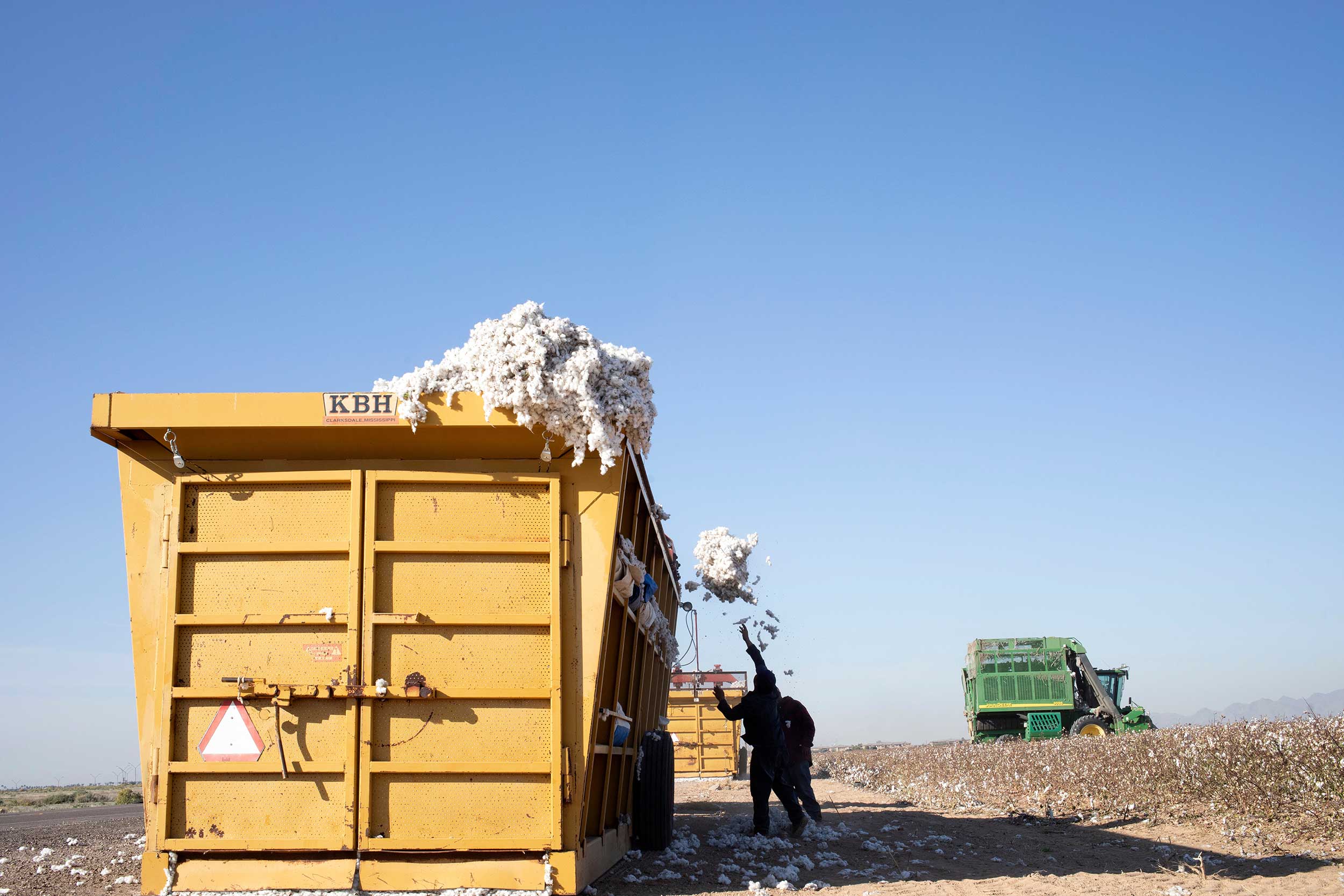
The biggest change came with the creation of a cotton seed from Monsanto that contained genes from Bacillus thuringiensis, a natural-born soil bacteria that causes the plant to produce insecticidal proteins to fight pink bollworm larvae.
This biotech advancement brought new, more sustainable practices for growers like Rayner in Goodyear.
Rayner’s family is well known for using no-tillage farming methods and a six-year rotational schedule with barley, alfalfa, and cotton to preserve soil health. In 1996, his first year of no-till, he also planted Monsanto seeds for the first time. He remembers walking into the cotton field and seeing spiderwebs everywhere on the plant stalks.
“Oh, this is crazy! Why are all these spiders here?” was his first thought. Then he realized that growers had been killing them, and spiders were an important predator of pests like aphids and whiteflies.
Transgenics made it easier to start no-tillage because RoundUp Ready cotton resisted the herbicide he used to clear everything else of weeds that would compete with the crop. With no weeds, he didn’t have to till the soil.
These technologies have made U.S. cotton cleaner and more sustainable when it comes to insecticide use. In the 1960s, cotton accounted for 40 percent of all pesticides applied in the U.S.; in 2008, its share was 7 percent.
A small move toward organic acreage
Every season, extension specialist and UA entomology expert Peter Ellsworth meets producers in the field to talk about integrated pest management and teach them how to identify beneficial insects or natural predators of cotton pests.
He sets traps with female boll-weevil pheromones to attract the males and then estimates their population in the field to ponder if it’s necessary to spray. Integrated pest management, unheard of before the 1990s, is now common practice among all cotton growers. Many use conventional IPM — they spray chemicals — but on rare occasions and in precise amounts to prevent resistance and use the least amount of pesticides.
The method was the cornerstone of the eradication program and allowed sensible decision-making. Too much chemical warfare will damage the soil and everything around it. Meanwhile, the bug will come back stronger. Even so, almost invariably, bugs develop resistance to the chemicals used to fight them.
“It’s not a matter of if but when,” said Paco Ollerton, a veteran cotton grower from Pinal County and the interim director of the Arizona Cotton Research and Protection Council.
In past years, the council’s focus has been on producing a product that combats a carcinogen fungus in farm soils. With that problem kept at bay, the council could gear up research and find alternatives to keep the bollworm and weevil at bay, Ollerton said.
Pest solutions are also being tested for organic cotton farming. Although currently only 1,200 acres in all of Arizona are farmed that way, certified organic farmland in Yuma could become the niche of a new cotton market.
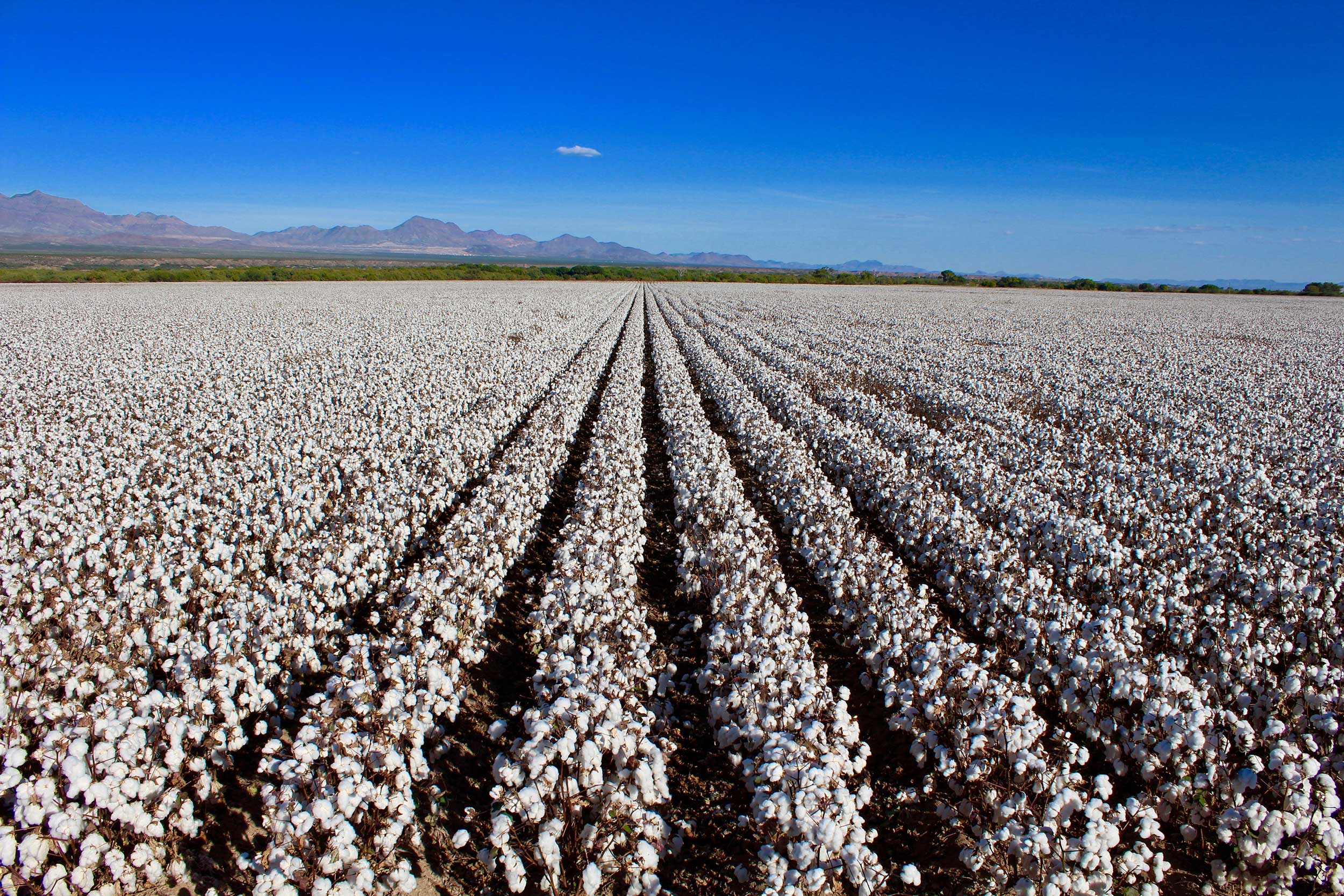
Thirty percent or so of the leafy greens and produce in Yuma County are already certified organic. That land is mostly unplanted in the summer and left exposed, which can decrease the health of crops, said Keith, a Ph.D. student in entomology and insect science at the UA.
Organic cotton could bring many positives, she said. The price for upland organic almost doubles conventional upland, so the crop would maximize farmer profits.
A survey distributed among pest control advisers and growers in the area showed 82% would support the shift. The biggest obstacles are finding an organic defoliant for the harvest and a bioinsecticide that is effective without hurting other beneficial insects. In conventional pest management, chemical application and timing have been perfected, something that is not well-studied for organic cotton farming. Keith is collecting data from the first trial and will run tests for a second season.
“There is a big knowledge gap. In conventional (farming) we have a lot of selective insecticides,” Keith said. “A lot of these organic chemistries that we’re working with, they’re not necessarily selective.”
Ed Curry, a chile grower from Pearce, grows about 100 acres of organic Pima cotton using drip irrigation. He said he doesn’t use any defoliant, even if it lowers the grade of his cotton. Because there is no organic gin for Pima cotton, he ships it to El Paso.
At that acreage level and point in time, is not profitable, he said: “I do it because I like it.” But he is fine-tuning it because it’s a low-water use crop — he uses 2 acre-feet a year using drip — that pays well.
“I love the challenge of organic,” he said. “And I think the future of ag will be moving to less chemicals.”
Can Arizona grow better seeds for the desert?
Jim Olvey is in the business of creating ever-better varieties of cotton. But it takes decades to produce them.
“When (farmers) pay for our bag of seed they are not paying for past research, they are paying for future research,” said Olvey, the president of American Pima Seed and of O&A Enterprises, a private breeding company.
It takes about 12 years to develop new varieties, he said.
Olvey and his son and business partner, Mike, grow about 1,000 acres of cotton every year to improve crossbreeding and select the best traits in plants. To save time, they also grow cotton in Costa Rica during the winter to get two generations in a year.
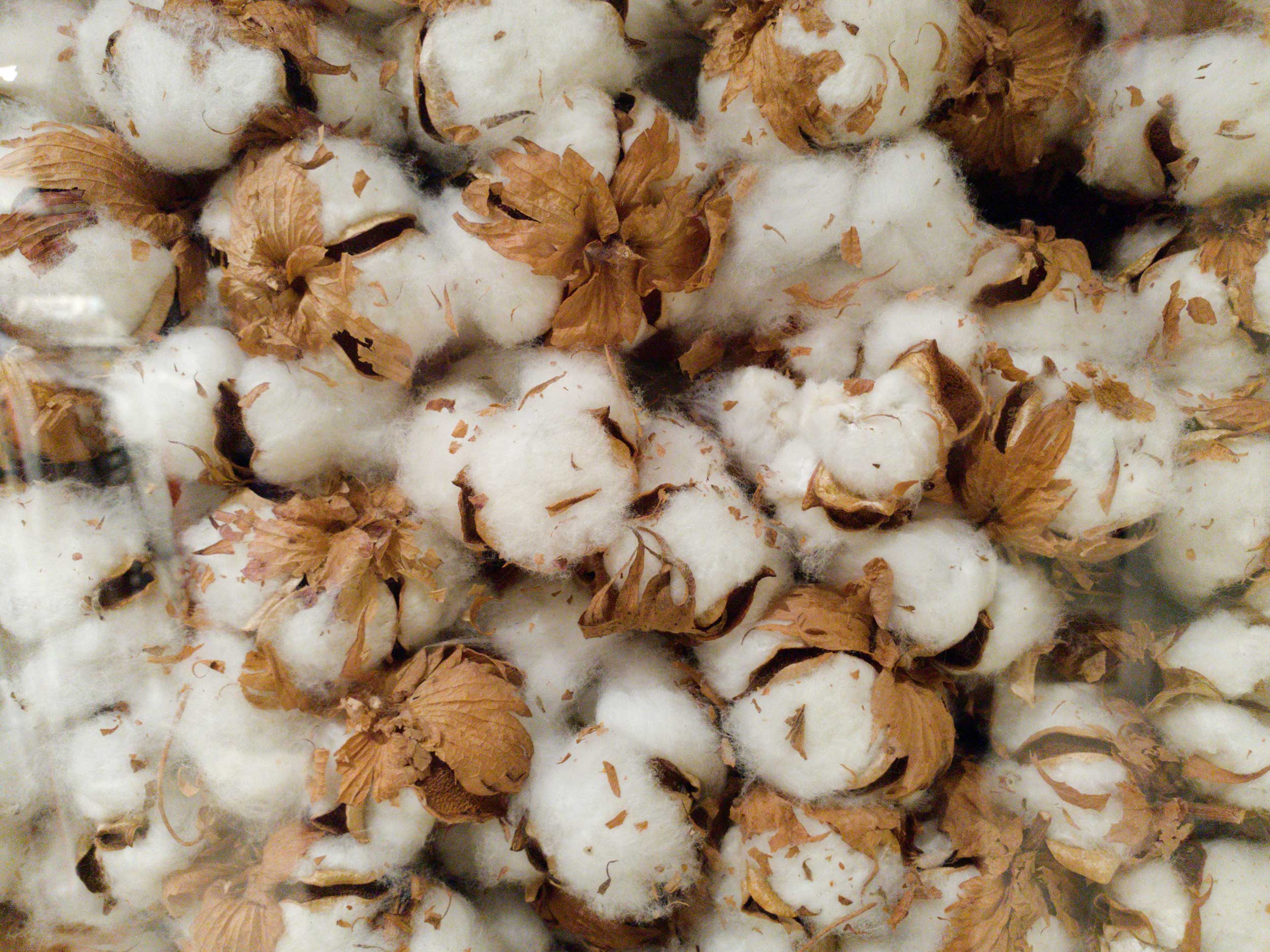
They’ve had to dedicate all their resources in the past five years to find a cotton variety that would resist Fusarium Race Four, or ROV4, a disease that could have wiped out the industry but never made it to Arizona. They’ve dedicated decades to all sorts of breeding projects, including growing colored cotton, in hues of brown, lilac and green.
Arizona is one of a kind because it is home to the largest cotton “seed bank.”
Inside a massive warehouse, stacks of plastic Tupperware containers, over 30 feet tall, hold a world of opportunities and “the tools of our trade,” said Olvey with pride. That place, with some 25,000 cotton varieties of cotton, is a collection that surpasses all others in China, India, France and even the USDA’s collection, half their size.
“Each [variety] has at least one thing distinctly about it,” said Mike Olvey, who joined his father in the business some 30 years ago. There’s even lint-less cotton, which has some other genes for cotton quality.
About 25 years ago, Jim saved 5,000 varieties of cotton from Russia, where post-Soviet economic depression placed the seed collection at risk because they couldn’t even pay for refrigeration. Ironically, many of those varieties had been collected in the U.S. decades before, and now they will help craft new varieties.
Mike Olvey said that even if cotton acreage continues to decrease, there should be an increase in the number of bales that come out of Arizona, maintaining quality.
“We’re just going to come up with better varieties that are going to use that water more efficiently. We’re going to get higher yields,” he said.